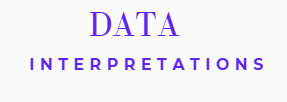
Digital Twins: Revolutionizing the Future of Technology and Innovation
A Digital Twin is a virtual model designed to accurately reflect a physical object, system, or process. By integrating real-time data and advanced simulation techniques, digital twins provide a bridge between the physical and digital worlds, enabling better monitoring, analysis, and optimization. The concept of digital twins has gained significant traction in recent years, particularly in industries such as manufacturing, healthcare, smart cities, and aerospace. As technology evolves, digital twins are set to revolutionize how organizations design, operate, and maintain systems, ultimately leading to greater efficiencies and innovation.
Origins and Evolution of Digital Twins
The concept of a digital twin was first proposed by Dr. Michael Grieves in 2002 as part of Product Lifecycle Management (PLM). At its core, the idea was to create a digital replica of a physical product to simulate its behavior and performance throughout its lifecycle. While early applications focused on engineering and product design, the emergence of the Internet of Things (IoT), cloud computing, and advanced data analytics has significantly expanded the potential of digital twins.
Today, digital twins are dynamic, interconnected models that go beyond mere replicas. They use real-time data from sensors embedded in physical assets, allowing the twin to mirror the state, condition, and behavior of the physical counterpart. This real-time connection enables predictive maintenance, optimization of processes, and informed decision-making.
Components of a Digital Twin
A digital twin comprises several key components:
- Physical Entity: The real-world object, system, or process that is being mirrored. This could be anything from a manufacturing machine, a jet engine, or even an entire smart city infrastructure.
- Digital Model: The virtual representation of the physical entity. This model is built using computer-aided design (CAD), simulation software, and data analytics. It mimics the characteristics and behavior of the physical object.
- Data Connection: Real-time data is collected from sensors on the physical entity and transmitted to the digital twin. This data allows the twin to constantly update and reflect the current state of its physical counterpart.
- Analysis and Simulation: Using the data, the digital twin can run simulations, perform analyses, and predict potential outcomes. This allows for optimization and problem-solving in real time without interfering with the physical asset.
- Feedback Loop: One of the most powerful features of a digital twin is its ability to create a feedback loop. Insights derived from simulations or predictions can be fed back into the physical system to enhance performance or prevent potential failures.
Applications of Digital Twins
The versatility of digital twins makes them applicable across a wide range of industries. Some of the most impactful applications include:
- Manufacturing
In the manufacturing sector, digital twins are used to optimize production processes, monitor equipment health, and reduce downtime. By simulating the production line, manufacturers can identify bottlenecks, test new configurations, and improve efficiency without disrupting actual operations. Predictive maintenance, powered by digital twins, allows companies to anticipate equipment failures and schedule repairs before breakdowns occur, reducing costs and improving productivity.
- Healthcare
In healthcare, digital twins can model human organs, medical devices, or entire healthcare systems. Personalized digital twins of patients enable doctors to simulate treatment plans, predict outcomes, and tailor interventions to the individual’s specific conditions. This opens up new possibilities in personalized medicine, where treatments can be customized based on real-time data from wearable devices or medical sensors.
- Smart Cities
Digital twins are increasingly being used to create smart city models, which help city planners manage infrastructure, energy consumption, and traffic flow. By simulating various urban scenarios, digital twins enable cities to plan for population growth, optimize resource distribution, and respond more effectively to emergencies or disasters.
- Aerospace and Defense
Aerospace companies like NASA and Boeing have been early adopters of digital twin technology. In aerospace, digital twins are used to monitor the health of aircraft engines, simulate space missions, and improve the design and performance of complex systems. For defense, digital twins can simulate battlefield conditions, optimize logistics, and improve decision-making.
- Energy Sector
In the energy sector, digital twins help manage power grids, wind turbines, and oil platforms. By continuously monitoring energy systems, digital twins can optimize energy consumption, detect inefficiencies, and reduce waste. Wind farms, for example, use digital twins to predict wind patterns, adjust turbine speeds, and maximize energy output.
The Benefits of Digital Twins
The use of digital twins offers numerous advantages across industries:
- Enhanced Efficiency: By simulating and analyzing real-world processes in a virtual environment, companies can optimize operations and reduce costs.
- Predictive Maintenance: Digital twins allow for early detection of potential issues, enabling companies to address problems before they result in costly downtime or failures.
- Improved Innovation: Digital twins enable rapid prototyping and testing of new ideas without the need for physical prototypes, speeding up the innovation process.
- Informed Decision-Making: Real-time data and simulations provide decision-makers with valuable insights that can guide strategic actions.
- Risk Mitigation: By simulating different scenarios, digital twins help organizations anticipate risks and develop contingency plans.
Challenges and Future Directions
Despite its potential, the widespread adoption of digital twins faces certain challenges. One significant hurdle is the integration of massive amounts of data from various sources, which requires robust data management and cybersecurity measures. Additionally, the creation of highly detailed and accurate digital models can be complex and costly, particularly for large-scale systems.
Looking to the future, the development of artificial intelligence (AI) and machine learning will further enhance the capabilities of digital twins. As AI algorithms become more advanced, digital twins will not only simulate physical systems but also learn from the data to predict trends and autonomously improve performance. The integration of 5G networks will also boost real-time connectivity and data transmission, making digital twins even more responsive and efficient.
Digital twins are transforming industries by providing a powerful tool for monitoring, optimizing, and innovating in real time. By bridging the physical and digital realms, digital twins enable organizations to make more informed decisions, reduce costs, and improve efficiency. As technology continues to evolve, digital twins will play a central role in shaping the future of industries ranging from manufacturing and healthcare to aerospace and energy. The rise of AI, IoT, and advanced analytics will further unlock the potential of digital twins, driving innovation and creating a smarter, more connected world.